*この記事はゴム・プラスチックの技術専門季刊誌「ポリマーTECH」に掲載されました。
特集1 押出成形・射出成形技術の最新動向
射出成形においてコンパウンド以外のアプローチで加硫時間を減らす方法はないのか
株式会社ケー・ブラッシュ商会 杉本圭
1 はじめに
ここではゴム射出成形プロセスを分析し、そして加硫時間短縮を妨げる限界を探ることを目的とし、 その後に限界を超えるための解決策や産業用途で使用される実例を交えながら紹介していく。
2 ゴム射出プロセス
ゴム射出プロセスにおいてコンパウンドはストリップ状態から押出機に入っていく室温から始まり、徐々に加熱され製品になりまた室温へ戻っていく温度変化をもつ。
いくつかのケースでは後加硫のためにオーブンへ入れるケースもあるが、これはあくまでも後加工でありここでは記載しないことにする。なお、温度変化は以下のような図1で表すことができる。
1)コンパウンド準備(押出):コンパウンドは可塑化され、最適な温度まで加熱される。この温度は次のステップをスムースに行うために計測されなければならない。
2)充填:射出チャンバー内に充填され射出準備OKとなる。このときの温度は一定でなくてはならない。
3)射出:ランナー内を流れる間にコンパウンドは加熱されていく。この加熱は主にシェアによるものだが、金型の外壁との接触による熱移動によっても温度は上昇していく。
4)加硫プロセス:キャビティ内が満たされた後もコンパウンドは金型温度まで達していないため、一定の温度になるまで加熱が続けられる。製品の厚みで加熱プロセスは短くも長くもなる。
5)冷却プロセス:金型から取り出した後も一定の冷却時間が必要になる。
3 加硫時間を短縮するために過去に何が行われてきたのか?
以下の方法が過去何年にも渡り行われてきた方法で品質の向上をもたらした。
1)スクリューとピストンの分離
押出条件の改善やコンパウンドの本当の温度を管理することにより、プロセスを最適化した最初のステップになる。
2)温度制御
正確な温度コントロールループは一貫した射出ユニット温度と金型温度保つために必要な技術である。金型に関してはヒーターとキャビティとの間には距離があり温度の違いが発生する。プロセスをコントロールするためにはキャビティを制御するのがとても重要で、制御ループを組むのは大変になるがプロセスに一貫性を持たすことができる。
3)金型温度バランス
金型の外側の面は熱を失う。これはエッジ効果と呼ばれ、側面や角の温度が中心部よりも下がってしまうことを指す。金型の温度は一番高い温度のキャビティに合わせなければならないが、加硫時間は低いキャビティに合わせる必要がある。この不均一な温度によって低いところはより時間をかけなければならなかった。Isothermouldはエッジ効果を解消するために開発され、すべてのキャビティ温を均一にすることができ、その結果加硫時間が短縮できる。
4)安全マージンの削減
より安全に品質をコントロールしてプロセスの振れ幅を補正するために、すべてのゴム製造業者は一定のマージンを加硫時間に加えている。
5)射出圧の増加
流れの中の層間で生じる摩擦がシェアを、そして熱を発生させて射出成型時にコンパウンドの加熱があることはすでに記載している。
より高い圧力であればコンパウンドの温度もより高くなるという事実がある。コンパウンド温度が高ければ下流の時間を短くすることが可能である。REPでは3000barまでの射出ユニットを持ち、加硫時間の短縮を可能としている。このアプローチは近年では一般的な方法とされ、現在もマーケットで宣伝されている。
しかし、この原理はコンパウンドがどれぐらいのシェアレベルを保持しているかによるという危険な面も含んでいる。もしシェアやコンパウンドストレスが高すぎる場合、製品の寿命を縮めたりキャビティに到達する前のランナー内でコンパウンドが焦げ付いてしまうリスクを高めることになる。
コンパウンド温度を過度のシェアによって上げすぎると、コンパウンド自体を痛め、パーツの質やゴムの寿命を縮めることになりかねない。
4 加硫時間短縮を妨げている物は何なのか?
射出成形中のゴムの流れを分析すると、シェアと材質の加熱温度が場所により違うことがわかった。この不均一さは過度のシェアやコンパウンドの劣化、スコッチによって引き起こされ、それが全体のウォーミングアップを阻害している。ただ、逆にシェアが少ない場所では射出段階において温度の上昇が緩やかになっている。この部分がコンパウンド全体の中で一番温度が低い場所になっており、最終的な加硫時間はこの温度に依存する。
4.1 ラミナーフロー効果
コンパウンドはランナーの内壁にくっついており(速度0)、その結果中心部分の流れが一番速くなる(図2)。シェアは層ごとの速度の違いによって起こりその結果摩擦が生じる。重なり合った層同士は速度差によって外側になればなるほど流れに大きなシェアと熱を持たせる。逆に内側の流れは隣り合った層同士はほぼ同じ流速でシェアや加熱も少しに抑えられている。その結果、外側は高温になり内側は低温を保つ状態が続くことになる(図3)。
このラミナーフロー現象は実際すべてのゴムの流れ、射出ユニット内、CRB内、また金型内で発生する。
そして特に金型内ではランナーゲート壁の熱がゴムの外側の流れに触れることでも温度上昇を招く。金型にあたる時間が長ければ長くなるほど内外の温度差が広がっていく。
計測はサーモカメラを用いて行い、NBR75Shの平均をデータとして使用した。射出ノズルから5mmの場所で温度差は10℃、250mm離れた箇所ではおよそ51℃にまで差が広がった。ランナーの太さはφ8mm。
ラミナーフローは内外が混ざり合うことはなく、金型内を流れる間常に差が開き続けて温度が不均一なままキャビティまで到達する。コンパウンドの一部の温度のみが加硫時間を決定する。それは一番低い部分の温度になる(図4)。
4.2 ランナースプリット現象
コンパウンドの外側の熱いゴムはランナーが分岐する際にほぼすべてが次のランナー内の内側を流れ、
中心部から流れるコンパウンド(冷たいコンパウンド)は次のゲートの外側を流れる。そして次の分岐点で暖かいコンパウンドは手前のキャビティへ、そして冷たいコンパウンドは外側のキャビティへと流れる。
各キャビティ内にコンパウンド温度差が生じる。すべての多数個取りの金型を扱うゴム製造者は完璧な金型温度と最適なランナーおよびゲートサイズを考慮してもキャビティを満たす際のアンバランスさを経験した(図5)。
それは温度が変わればキャビティを流れるコンパウンド粘度も変わってしまうからである。このアンバランスを調整するための共通の方法はゲートサイズの調整とゲートを流れる量を絞ることだったが、流れるゴムの量を調整することはできても温度のアンバランスは解消できなかった。
数個のキャビティが加硫時間を決める。:温度の低いコンパウンドのキャビティ。
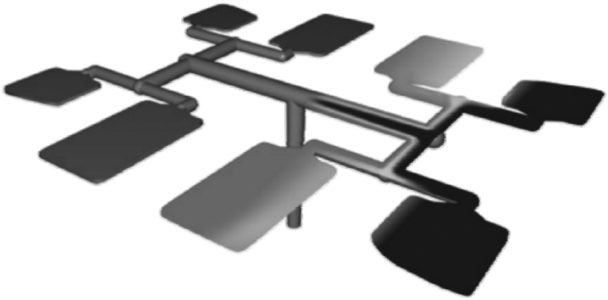
図5 多数個取りの金型内におけるコンパウンド温度
5 解決策
加硫時間は中心部のゴムによって決まり、制限は外側のゴムによって決められる。
TurboCure® (ターボキュア)と呼ばれる技術は三つの異なったモジュールから成り立っている。それは、TempInverter®(ノズル技術) 、FillBalancer®(金型ランナー技術)、FillBalancer® Max(金型キャビティ手前技術)である。
5.1 TempInverter® (特許出願中)
最初の解決策は中心と外側の流れを入れ替える方法である。このTempInverter®といわれる技術は外側のコンパウンドを中心に流し、中心のコンパウンドを外側に流す。このシステムはノズルの直前に設置され中心部の温度を約10度上昇させることができる。中心部の温度を上げることで加硫時間を短縮できる(図6)。
5.2 FillBalancer®
(特許番号 6.077.470 & 6.503.438)
ランナーの分岐でのアンバランスとは分岐での温度不均一のことで、コンパウンドの流れを動かすことにより次のランナーでも均一な温度分布を得ることができる(図7)。
ランナー分岐点で2次元方向から来る流れを下から通すことで温かいゴムが側面ではなく底面にたまるようになる。その結果、次の分岐点で左右に均一な温度分布で流れていく。
ランナー内の温度分布を動かすことで枝分かれした際に同じような状態を保つことができ、キャビティ内の温度バランス、流量バランスを向上させることができる。
低い温度のキャビティをなくすことで全体の加硫時間が短縮される。
FillBalancer®はBeaumont Technology Inc.の世界特許を使用しており、これは元々樹脂に数年前から使われている。MeltFlipper®と呼ばれているこの形状は、金型の構成に大きく依存し、スプルー分割効果、キャビティの数、およびランナーの形状に応じて変化する。Beaumont社はこれらの形状の設計に大きな経験を持ち、REP社はゴム製の特異性のためのノウハウを持っている。そして与えられたアプリケーションに最も適した形状のデザインと、この技術のために必要なライセンスの供給を組み合わせたソリューションを提供する。
■充填バランス改善の利点
熱バランス改善の利点は加硫時間短縮になるが、充填バランスにおいても多大なメリットをもたらす。アンバランスが起こっているとき、最初に充填されたキャビティでは他のキャビティに充填するための圧がかかり続ける。その結果、フラッシュが起こったり、コンパウンドがはみ出るといった現象が起こりやすくなる。このようなパーツは頻繁にバリ取りを行う必要があり、
全文:約6676文字